MEDICAL AIR
GUIDELINES FOR THE PRODUCTION OF MEDICAL AIR AT THE HOSPITALS
If medical and synthetic air, as described by the European Official Pharmacopeia, is produced on the hospital premises, be them private or public, it is considered as a pharmaceutical product. It is therefore produced by the hospital pharmacy and should be used within the hospital premises. Hence, the hospital pharmacy is to be held accountable for its production and must guarantee that its quality complies with medical instructions on medical air, oxygen and nitrogen for pharmaceutical use. Quality must be guaranteed both when working with compressed air and oxygen-nitrogen mixtures containing from 20% to 23.5% of oxygen. The description of the systems to produce medical air in hospitals has to take into account the use of such systems, which are connected to a gas pipeline sys-tem supplying the whole hospital with medical air. Medical air pipeline systems and production units are medical devices, as established by Directive 93/42 (Decree-Law 46/97). Medical gas pipeline systems are regulated by the harmonised European EN Standard 7396-1. Two main factors distinguish these systems from the ones used by medical gas suppliers: a) The need to ensure a constant supply to the pipeline system, as established by the harmo-nised UNI EN Standard 7396-1. b) The need to ensure the air flow required by the pipeline system at all time, as established by the harmonised UNI EN Standard 7396-1. Furthermore, the pipeline system demands a specific supply pressure, which needs to remain constant, regardless of the flow provided by the pro-duction unit.
MEDICAL AIR OBTAINED BY COMPRESSION
A Medical Air Plant equipped with compressors usually features one or multiple sets of compressors, one or multiple air treatment systems, one or multiple tanks. The materials coming in contact with air (espe-cially non-metallic materials and lubricants, in case any are used) should not cause any contamination beyond the limits indicated by the European Official Pharmacopoeia. Compressor-based systems should include a constant monitoring of humidity (water vapour < 67 V/V). Moreover, they should be equipped with a sample exhaust to enable a periodic measurement of: • carbon dioxide < 500 ppm; • carbon oxide < 5 ppm; • sulphur dioxide < 1 ppm; • nitrogen oxides < 2 ppm; • oil < 0.1 mg/m3.
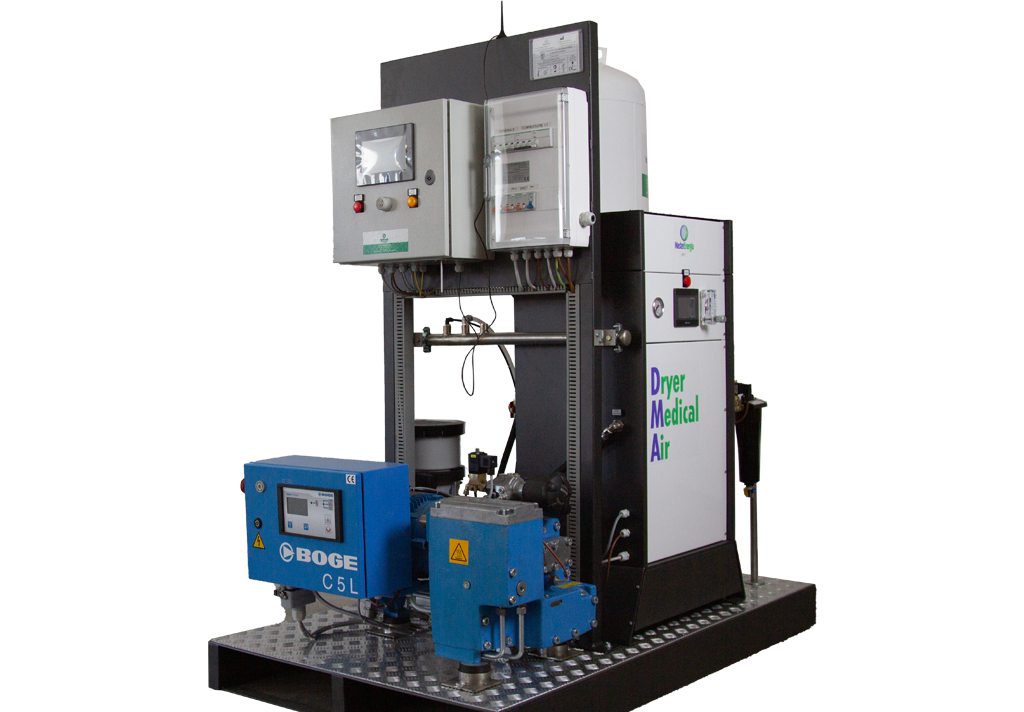
Monitoring humidity is of utmost importance, as this value is evidence to the proper functioning of the air treatment system. Furthermore, it determines the development of microorganisms in the pipes of the pipeline system.
If the air is used to activate surgical equipment, a high level of humidity can rapidly disable the small components coming in contact with the air and rotating at high speed.
Compressor-based systems should be equipped with alarms to notify users when:
– the compressors’ values are no longer within the range set by the manufacturer;
– the air treatment system’s values are no longer within the range set by the manufacturer;
– humidity is over the set value;
– the production unit’s outlet pressure is below the minimum value required by the pipeline system.
The safety requirements regarding compressors are indicated in UNI EN Standard 1012-1.
MEDICAL AIR RECONSTITUTED BY A MIXTURE OF OXYGEN FU AND NITROGEN FU
Breathing air for medical applications must have a high level of purity to guarantee the health of patients. A Medical Air Plant for the production of reconstructed medical air will be equipped with a mixer, a tank, one or multiple analysers and a shut-off valve at the bottom of the tank. By means of an analyser, the system needs to guarantee a constant monitoring of the oxygen level in the oxygen-nitrogen mixture, which needs to range from 20% to 23.5%.
Systems equipped with a mixer have to include alarms to notify the following anomalies: • the mixer’s values are no longer within the range set by the manufacturer; • the oxygen level in the oxy-gen/nitrogen mixture is not within the limits indicated by the Italian Official Pharmacopeia. As a re-sult, the signal activating the alarm will automatically act on the control valve, causing the mixer to be isolated; • the production system’s outlet pressure is lower than the minimum pressure required by the pipeline system.